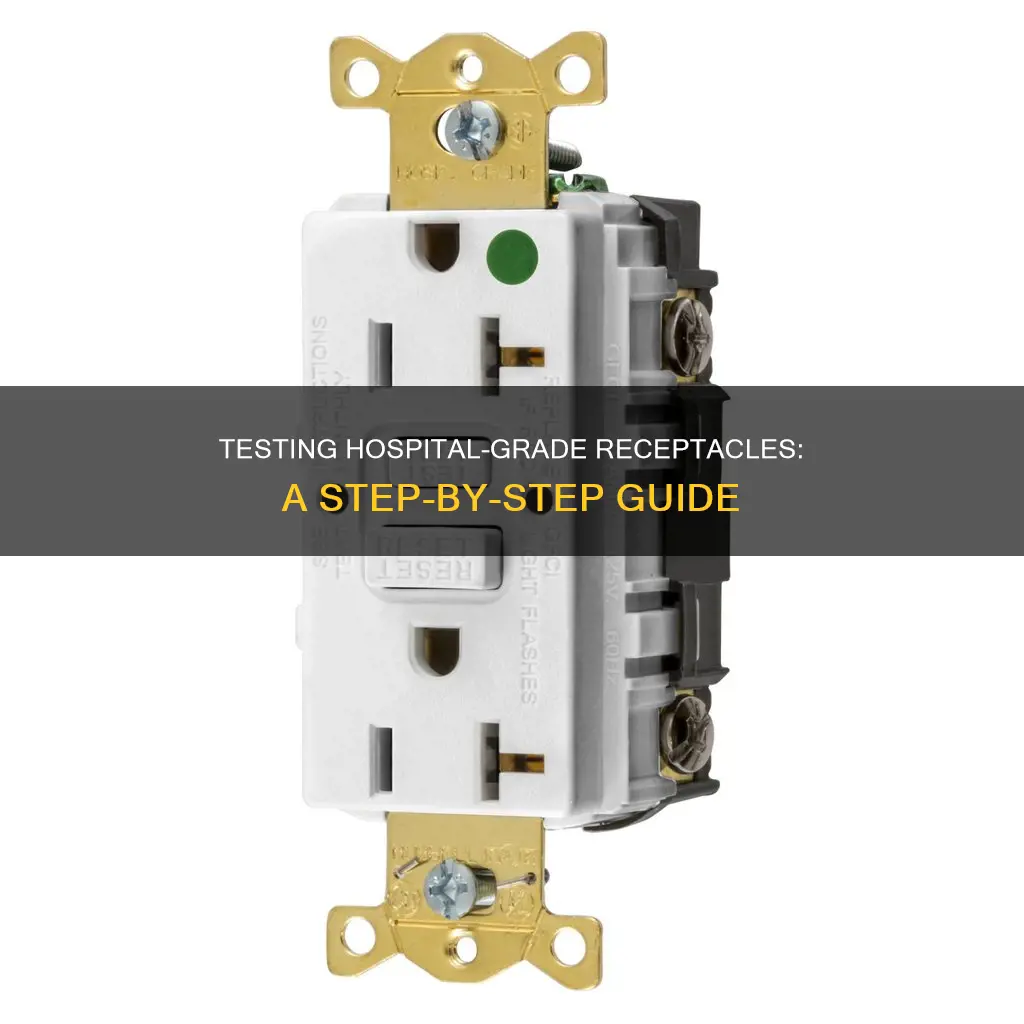
Hospital-grade receptacles are required in patient bed locations of general care areas to ensure that a receptacle with a stronger grip can prevent attachment plugs from slipping out of the socket. These receptacles are identified with a green dot and the words hospital-grade stamped on the device. They are also required in anesthetizing locations. Testing of hospital-grade receptacles is done with a digital analyzer and should be performed by facility staff with the knowledge and equipment to do so. The tests include verifying the physical integrity of the receptacle, the continuity of the grounding circuit, and the correct polarity of the hot and neutral connections. The receptacles must also pass a certain amount of pull force on the plug before it comes out.
Characteristics | Values |
---|---|
Testing standard | NFPA 99, Health Care Facilities Code, 2012 edition |
Testing frequency | Hospital-grade receptacles must be tested after initial installation, replacement or servicing of the device. Non-hospital-grade receptacles must be tested annually. |
Testing entity | Testing can be completed by facility staff as long as they have the knowledge and equipment to perform the tests. |
Location | Patient bed locations of general care areas, critical-care areas, and anesthetizing locations. |
Purpose | To ensure a receptacle with greater contact tension is provided to minimize the possibility of an attachment plug supplying medical or life support equipment being disconnected. |
Identification | Hospital-grade receptacles are identified with a green dot on the face of the receptacle, and the words "hospital-grade" are usually stamped on the device's mounting strap. |
Power strips | Power strips must be UL listed and hospital grade, adequate for the number and types of devices, not overloaded, and must not be daisy-chained. |
What You'll Learn
- Testing hospital-grade receptacles after installation, replacement or servicing
- Testing non-hospital-grade receptacles in patient areas
- Ensuring receptacles have stronger prongs to prevent accidental disconnection
- Testing receptacles in patient care rooms
- Testing receptacles in long-term care facilities
Testing hospital-grade receptacles after installation, replacement or servicing
Testing hospital-grade receptacles is essential for ensuring patient safety and maintaining the proper functioning of medical equipment. Hospital-grade receptacles differ from commercial or residential-grade receptacles in that they have stronger "prongs" on the inside, which help to prevent cords from accidentally falling out. This feature is crucial for medical and life support equipment, as a disconnection could have life-threatening consequences.
According to the National Fire Protection Association's (NFPA) guidelines, hospital-grade receptacles must be tested under specific circumstances. Section 6.3.4.1.1 of the NFPA 99-2012 guidelines states that hospital-grade receptacles must be tested after initial installation, replacement, or servicing of the device. This testing ensures that the receptacles are in proper working condition and meet the required safety standards.
The testing process typically involves verifying the physical integrity of each receptacle and ensuring it meets the necessary standards. This may include checking the force of the prongs, which should be no less than 4 ounces, to ensure that cords cannot be easily dislodged. Testing may also involve electrical outlet testing, which can be completed by facility staff provided they have the necessary knowledge and equipment.
While hospital-grade receptacles are not subject to annual testing requirements, the frequency of testing is based on performance data. This data includes the manufacturer's recommendations, which should be carefully followed to ensure the receptacles are maintained in optimal condition. It is important to note that receptacles in patient bed locations and areas where deep sedation or general anesthesia is administered are subject to more stringent testing requirements, with tests required at intervals not exceeding 12 months, according to section 6.3.4.1.3 of the NFPA 99-2012 guidelines.
By adhering to these testing guidelines, healthcare facilities can maintain the proper operation of devices during emergencies and enhance electrical safety for patients, their families, and staff members.
Post-Hospital Care: Looking After Yourself at Home
You may want to see also
Testing non-hospital-grade receptacles in patient areas
The physical integrity of each receptacle must be verified, and they should only be used for movable patient care medical equipment. Power strips, for instance, must adhere to specific guidelines: they must be UL-listed and hospital-grade, adequate for the connected devices without being overloaded or daisy-chained, and they should not present a trip hazard.
It is important to note that the NEC generally does not require hospital-grade receptacles for exam rooms in medical buildings. However, owner or engineering specifications may be more restrictive, and hospital-grade receptacles may be specified as a design requirement. Hospital-grade receptacles are identified by a green dot and the words "hospital-grade" stamped on the mounting strap.
The primary reason for using hospital-grade receptacles at patient bed locations is to ensure greater contact tension, reducing the chances of an attachment plug supplying medical or life support equipment from accidentally disconnecting. Hospital-grade receptacles have stronger "prongs" inside to prevent cords from falling out, which could be life-threatening in certain situations.
To summarise, while non-hospital-grade receptacles in patient areas must be tested annually, hospital-grade receptacles are tested based on performance data and manufacturer recommendations. This testing regime helps maintain the functionality and safety of electrical systems in healthcare facilities.
Detecting Testicular Cancer: Hospital Examination Procedures
You may want to see also
Ensuring receptacles have stronger prongs to prevent accidental disconnection
Hospital-grade receptacles are designed to withstand much more abuse than a regular outlet and feature stronger internal prongs to grip equipment and prevent accidental disconnection. This is particularly important in a hospital setting, where equipment such as life support machines must remain securely connected to power at all times.
Hospital-grade receptacles are identifiable by a green dot and are typically installed with the ground prong facing upwards. This is because, in the event that a plug is accidentally pulled or tripped over, the ground prong, being at the top, will be the last to come out due to gravity, thus minimising the chances of accidental disconnection.
To ensure that hospital-grade receptacles are functioning correctly and providing a secure connection, regular testing is required. The National Fire Protection Association's National Electrical Code, Article 517, outlines specific requirements for electrical equipment within patient care areas, mandating the use of hospital-grade receptacles. The 2012 edition of the NFPA 99 Health Care Facilities Code, serves as the testing standard, requiring initial testing after installation, replacement, or servicing. Additionally, receptacles in patient bed locations and areas where deep sedation or general anaesthesia is administered must be tested at intervals not exceeding 12 months.
To further enhance electrical safety and ensure the proper operation of devices during emergencies, healthcare facilities should develop policies adhering to the Occupational Safety and Health Administration Standard 29 CFR 1910 Subpart S. Power strips in patient care areas should also comply with specific guidelines, including being UL-listed, adequately rated for connected devices, and regularly verified through preventive maintenance.
Superbugs in US Hospitals: A Common Concern?
You may want to see also
Testing receptacles in patient care rooms
Understanding Hospital-Grade Receptacles
Hospital-grade receptacles differ from commercial or residential ones in their construction and performance requirements. They are designed to prevent attachment plugs from easily slipping out, ensuring a secure connection for medical equipment. These receptacles have stronger "prongs" or "grounding contacts" with greater contact tension, enhancing grounding reliability and reducing the risk of accidental disconnection.
Testing Procedures and Standards
The National Fire Protection Association's (NFPA) NFPA 99, Health Care Facilities Code, serves as the standard for receptacle testing. According to Section 6.3.4.1.1, hospital-grade receptacles must be tested after initial installation, replacement, or servicing. Section 6.3.4.1.3 specifies that receptacles in patient bed locations and areas where deep sedation or general anesthesia is administered must be tested at intervals not exceeding 12 months.
Patient Care Room Considerations
When testing receptacles in patient care rooms, it is essential to ensure compliance with Occupational Safety and Health Administration (OSHA) standards and the National Electrical Code® (NEC). The NEC, in Article 517, requires a minimum of four hospital-grade receptacles in patient bed locations within general care areas, as indicated in 517.18(B). For critical care areas, as per 517.19(B)(2), a minimum of six receptacles are mandated. Examining rooms, however, typically do not qualify as patient bed locations and are excluded from the hospital-grade requirement.
Power Strip Guidelines
Power strips in patient care rooms must adhere to specific guidelines. They should be UL-listed, hospital-grade, and adequate for the types and number of devices connected. Daisy-chaining power strips (interconnecting them) is prohibited to prevent overloading and trip hazards. Power strips should exclusively power movable patient care medical equipment and be listed as UL 1363A or UL 60601-1. Regular verification, documentation, and maintenance are crucial to ensure safety and compliance.
Testing Protocols
The physical integrity of each receptacle in patient care rooms must be confirmed through testing. This includes verifying the strength and durability of the receptacles and their ability to withstand a certain pull force on the plugs. Testing should also encompass ground testing to ensure proper grounding connections, which is of paramount importance in a hospital setting.
Effective Techniques for Removing Hospital Casts
You may want to see also
Testing receptacles in long-term care facilities
Understanding Hospital-Grade Receptacles
Hospital-grade receptacles are designed with enhanced features to meet the demanding requirements of healthcare settings. They are typically identified by a green dot on the face and the words "hospital-grade" stamped on the mounting strap. These receptacles have stronger internal prongs with higher retention grip to prevent plugs from accidentally slipping out. This feature is crucial for ensuring the continuous operation of life support equipment and other critical medical devices.
Regulatory Standards and Requirements
The National Fire Protection Association's (NFPA) NFPA 99, Health Care Facilities Code, serves as the primary standard for receptacle testing in long-term care facilities. According to Section 6.3.4.1.1 of the 2012 edition, hospital-grade receptacles must be tested after initial installation, replacement, or servicing. This ensures that they are in proper working condition and meet safety standards.
Additionally, Section 6.3.4.1.3 of the NFPA 99-2012 standard specifies that non-hospital-grade receptacles in patient bed locations and areas where deep sedation or general anesthesia is administered must be tested regularly, with intervals not exceeding 12 months. This ensures that even non-hospital-grade receptacles in critical areas are maintained and safe for use.
Testing Procedures and Frequency
The physical integrity of each receptacle in patient care rooms should be verified. This includes inspecting for any damage, corrosion, or wear and tear that may compromise the functionality or safety of the outlet. The force of the prongs is also tested to ensure they meet the minimum standard of 4 ounces, preventing plugs from accidentally falling out.
While hospital-grade receptacles are not subject to annual testing like their non-hospital-grade counterparts, their testing frequency is based on performance data. This data includes manufacturer recommendations, the history of the receptacle's performance, and any relevant maintenance records. It is important to follow these guidelines and industry best practices to ensure the safe and effective operation of all electrical receptacles in long-term care facilities.
Testing Personnel
Electrical receptacle testing in long-term care facilities can be completed by facility staff, provided they have the necessary knowledge and equipment to perform the tests accurately. However, it is important to ensure that staff members are properly trained and equipped to handle the testing procedures, as outlined by industry standards and safety regulations. Alternatively, long-term care facilities can engage the services of professional electricians or specialists who are experienced in conducting such tests and can provide expert advice on receptacle maintenance and safety.
PCA Machines: Standard Hospital Equipment?
You may want to see also
Frequently asked questions
Hospital-grade receptacles are identified by a green dot on the face of the receptacle and the words "hospital-grade" stamped on the device's mounting strap. They have stronger "prongs" on the inside to help prevent cords from falling out of the socket.
Hospital-grade receptacles are not required to be tested annually. Instead, the frequency of testing is based on the performance data, such as the manufacturer's recommendations. They must, however, be tested after initial installation, replacement, or servicing of the device.
Non-hospital-grade receptacles in patient care rooms and anesthetizing locations must be tested annually.
Hospital-grade receptacles are required in patient bed locations of general care areas, with a minimum of four receptacles. In critical care areas, a minimum of six receptacles are needed.